The Unseen Problem with Batteries: Hardwired & Inflexible
All electronic devices require some form of electrical power...
Stephen Horowitz & Seth Price
11/14/20239 min read
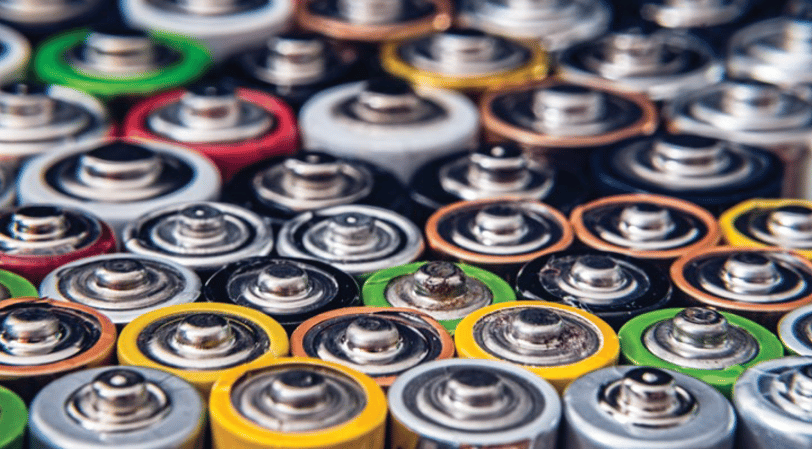
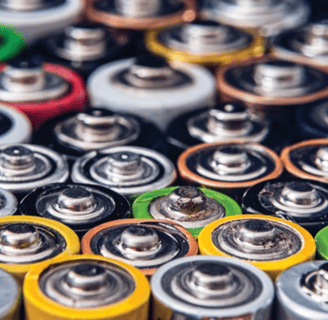
For example, consider the inrush current required to start an electric motor. To start this motor from a battery, the battery must be able to supply a large current at the beginning of the cycle, even though it will not need to maintain this current through the motor’s operation. Therefore, the battery system must be con gured to provide this starting inrush current.
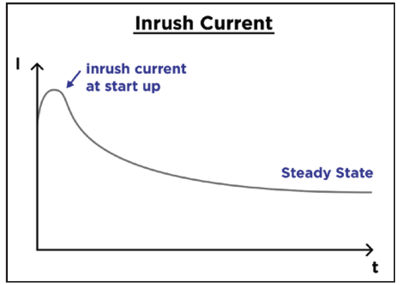
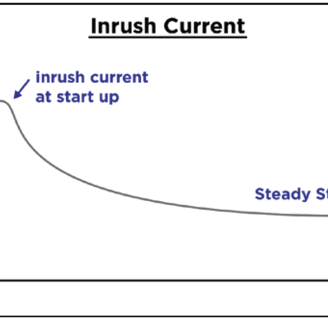
All electronic devices require some form of electrical power. Many devices use stored energy in batteries to deliver power to the load. While batteries are o ered in standard sizes, sometimes the application requires a custom power pro le for transient power demands, or variable loads with respect to time.
Hard-Wired Battery Configurations
When the average person thinks about batteries, they think about replacing standard-sized batteries, such as AA or AAA in a small electronic device. Typically, these batteries are hardwired in some combination of series or parallel circuits.
When batteries are placed in series, they are stacked so that electrons ow from the positive side of the battery, through the negative side, then into the positive side of the next battery, then out the negative side, and so on. Taken as a whole, the voltages of these batteries stack. For example, two 1.5 V AA batteries placed in series can generate 3 V of potential.
Series Batteries
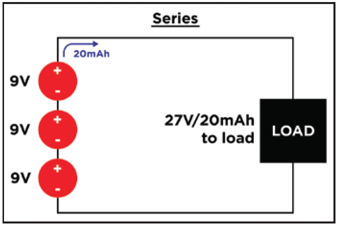
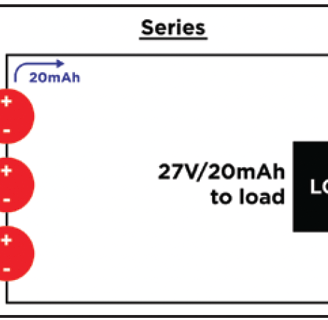
Parallel Batteries
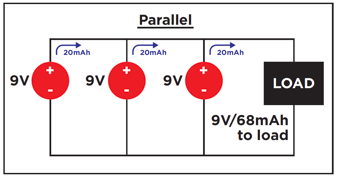

When batteries are placed in parallel, the positive terminals of both batteries are connected together and the negative terminals of both batteries are connected together. With parallel con gurations, the voltage remains the same, but the current adds. Two 1.5 V AA batteries placed in parallel will have only 1.5 V of potential, but can deliver twice as much current as one battery alone.
Combination of Series & Parallel Circuits
To meet the voltage and current requirements of many devices, engineers will design systems with parallel stacks of series batteries. Often, this is over-designed, so that there are more parallel branches to ensure that peak currents can be delivered during startup, even though the high current load is not required for normal operation.
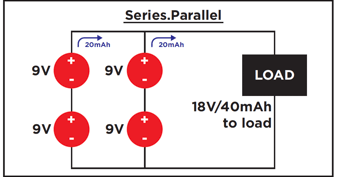
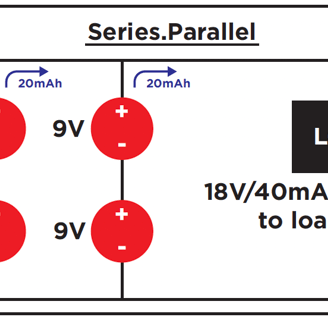
Limitations with Hardwired Battery Configuration
Series, parallel and combination battery circuits all share one common problem: they are hardwired. This means they are static, locked into a fixed confguration from the factory. They are often over-designed to deliver the current at startup, ine cient at charging and discharging, and have numerous other limitations.
Electrochemistry dictates the output voltages available for batteries. From there, there can only be an integer number of batteries, leading to nite possibilities for output voltage. For example, AA batteries can only output 1.5 V. If they are stacked in series, they can output 1.5 V (1 x 1.5V), 3 V (2 x 1.5V), 4.5 V (3 x 1.5V) and so on. If another voltage is required, say 5 V, the circuit must include a step down transformer, buck converter, linear converter or some other method of changing the voltage and current to re ect the demands of the system.
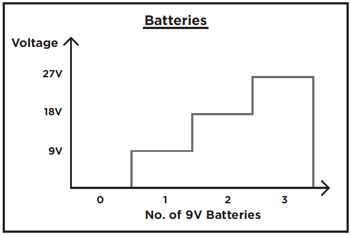
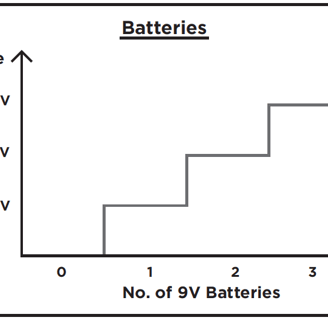
Limited Options for Output Voltage
These components are hardwired as well, meaning a system that requires 5 V needs to always require 5 V, it cannot be changed while in operation. However, the real world does not operate so statically, and voltage loads and demands can change arbitrarily or periodically. Instead, a compromise is made, often at the expense of e ciency and through the generation of heat or higher currents. Hardwired battery con gurations simply lack the versatility to meet rapidly changing load conditions.
Battery Charging Limitations
Consider an AC signal used to charge a battery. A 120 V AC varying at 60 Hz must be converted to a DC signal through a recti er circuit and perhaps a large capacitor to reduce the ripple voltage. The bigger the capacitor, the heavier, but the smaller the ripple voltage. Besides adding weight and taking up more space, only small portions of the sinusoidal input voltage are useful during the charge cycle. All of this is ine ciency built into the battery charger that has been generally accepted as the cost of doing business.
A Low Dropout Voltage (LDO) regulator can help this problem a little. Suppose a battery charging system is outputting 3.6 V, with some ripple voltage and noise. An LDO regulator may be able to stabilize the output voltage with little ripple at 3.0 V. However, the larger the di erence between the input and output voltage, the more heat is generated, so LDO regulators are only useful for low power applications.
Battery Variation
Many systems that use multiple batteries run into the problem that every battery will be slightly di erent. Some of these batteries will be weaker than others. If one battery discharges faster than the others, eventually, it will be the one to fail.
In a sealed package of ten series connected batteries, one failed cell is enough to make the rest of the pack worthless, as one failed battery prevents the ow of current. One option is to include a Battery Management System (BMS) that monitors the health of different cells in a battery. A BMS can detect temperature changes in cells and look for thermal runaway events, or detect if one cell is weak. The primary di erence between a BMS and electronic battery switching is that a BMS has few options once a problem is detected. It can do some battery balancing, but it cannot recon gure the battery stack to work around a weak cell.
Software-Controlled Battery Switching
Instead of relying on hardwire con gurations and over-design to deliver the power needs, what if there was an adaptive system that changed battery con guration electronically? With software-controlled battery switching, the connections between the battery terminals can be switched electronically to provide the proper power requirements without having to manually rewire all of the batteries.
Smart Charging and Discharging Cycles
When a stack of batteries requires a charge, it is advantageous for them to be connected in parallel. This way, the charging source voltage is applied to all cells, and, due to Kirchho 's Voltage Law, are trying to reach the same, fully charged state. However, when a fully charged battery is discharged through a source, it may bene t from the full potential of a series connection. In this way, the same four 1.5 V AA batteries can be charged using 1.5 V, but then deliver 6 V of potential when connected in series. With software-controlled battery switching, both of these are possible, as the controller will shift the states of the electronic switches to connect them as needed, for charging and discharging cycles.
Consider the application where a laptop is plugged into a wall while its user plays with the device. It is charging and discharging at the same time. Smart control of the device can optimize the interconnects to provide just the right amount of power at any given time. This has the potential to save energy as well as wear and tear on the charger and battery stack.
Arbitrary Waveforms
By using a software-controlled battery switching device, the voltage and current outputs of a battery stack can be rapidly changed. Through software, an arbitrary waveform can be generated.
Standard arbitrary waveform generators require an AC power input, a wave chopping circuit regulators, transformers, and various other components. With a software-controlled battery switching unit, the interconnections between the batteries are changed, which changes the output voltage and current, which can then generate a waveform as required by software. This arbitrary waveform can be programmed by an engineer for the application, or used in a feedback loop to supply the proper power requirements on demand.
Voltage and Current Transformation
With hardwired devices, there is no exibility when converting from DC to DC, DC to AC or AC to DC. The electronics are designed before the product hits the market, the components are xed, and the device is only capable of performing the original task. With software-controlled battery switching, the same device can perform DC to DC, DC to AC, and AC to DC switching, depending on the requirements of the system. Consider a small solar panel that is used for powering devices in a remote location. The cell is generating a DC voltage and converting it to another DC voltage for storage in the battery. Then, the battery is used to power an AC power tool using a DC to AC inverter. Perhaps an operator needs to charge their smartphone at the site, requiring a di erent DC to DC conversion, or worse, converting DC to AC in the inverter to run a wall-wart converter, which is ine cient. With software switching, all three of these tasks can be performed with the same device, saving space and reducing costs.
Benefits
The primary benefits of a software-controlled battery switching system are the weight savings, energy savings, and the ability to vary the voltage and current output of the battery system using software control, though other bene ts will be realized through the widespread implementation of these systems.
Weight Savings
Software-controlled battery switching allows for con gurable voltage output. With this system, engineers do not have to “over-design” a system to meet high inrush currents at startup as well as the larger voltage requirements during runtime. This means fewer batteries are required for the same performance.
One of the major drawbacks with electric vehicles is the need to store large amounts of energy. Every added battery is added weight, reducing cruise distance. This applies to more than just passenger vehicles; drones, autonomous mobile robots (AMRs), collaborative robots (cobots) and other mobile applications can bene t. Furthermore, the reduced weight in power tools can minimize fatigue for construction workers, assemblers, and weekend warriors.
Energy Savings
There are numerous ways that software-controlled battery switching can save energy. Smart charging and discharging cycles that can be optimized for e ciency, battery life or rapid energy delivery are just the start.
Software Control
Battery connections are controlled via software, meaning an in nite number of possibilities are available, because connections can also be changed dynamically in real time, responding to needs as they arise.. Unlike hardwired connections, software can process feedback from other parts of the system and adjust the output voltage and current accordingly.
One possibility out of many is a modified Pulse Width Modulation (PWM) routine. In traditional PWM, the duty cycle of a signal is changed to produce the desired e ect. It switches the power o and on for the correct amount of time and at the right frequency to emulate the proper power requirements. With software-controlled battery switching, batteries can be switched from parallel to series, with a controlled duty cycle between them, meeting this power requirement as well as adjusting to the actual capacity of the batteries as they discharge. The end result is a much more stable power supply than could be expected from PWM alone.
Eventually, this software control could be paired with arti cial intelligence (AI) to self-diagnose and deliver the correct power required, potentially anticipating surges in demand or periods of deep cycle charging are appropriate.
The Future of Electronic Battery Switching
As these systems come to market, more practical applications will be developed. There are already obvious advantages in the renewable energy, portable charging and electric vehicles markets.
Renewable Energy
Renewable energy sources, such as wind and solar, require additional energy storage to increase their e ciency. Batteries offer energy storage, but their charging and discharging cycles are not optimal, reducing the overall e ciency. Therefore, renewable energy systems are sometimes regarded as a “backup” or “supplemental” power source, depending on whether the wind is blowing or the sun is shining.
Enter electronic battery switching. Solar panels and wind turbines generate a DC voltage that can be applied to batteries in parallel at the appropriate voltage, but then discharge in series when the demand for energy decreases. Also, instead of a static battery bank, the software-controlled battery system can adjust to protect the weakest battery in the system, pick which batteries are used at a particular time, and produce clean, sinusoidal voltage on demand.
Portable Charging
Portable electronic devices, such as smartphones, tablets and laptop computers are limited in their battery life. While charging technology has improved over the past decade, the fact remains that anything that can be done to use less energy during the charging cycles of these devices is an improvement.
Consider the laptop that sits plugged in for most of the day, or the smartphone that is plugged in all night. The electronic battery switching device can optimize this charging and discharging cycle, leading to longer battery lifetimes, less energy used, and less heat generated.
Electric Vehicles
Electric vehicles will not only benefit from the weight savings, but they will also bene t from smart charging, made possible only through software-controlled switching. They will use less energy during their charging cycles, can prevent damage to weaker cells in the battery, and extend the overall lifetime of the batteries.